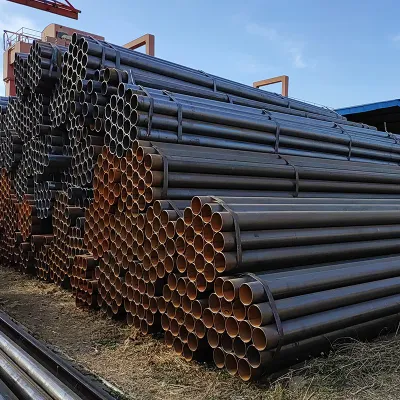
Aluminum tubing is widely used in various industries due to its lightweight and corrosion-resistant properties. Whether it's for automotive, aerospace, or HVAC applications, proper joining of aluminum pipes is crucial to ensure structural integrity and performance. With the increasing demand for aluminum tubing, it becomes essential for manufacturers to understand and implement proper soldering techniques for joining aluminum pipes.
Dongguan Zanci Pipe Co., Ltd. is a professional non-ferrous metal pipe manufacturer with a focus on producing high-quality aluminum pipes. Established in 1984, the company has grown to become one of the leading precision pipe manufacturers in China, specializing in the production of non-ferrous metal pipes, including brass pipes, copper pipes, bronze pipes, copper-nickel pipes, and aluminum pipes. The company's dedication to quality is evident through its strict adherence to ISO9001 standards and the production of products that meet ASTM, EN, BS, JIS, and GB standards.
In the manufacturing process of aluminum tubing, properly joining aluminum pipes through soldering is crucial to ensure the overall quality and performance of the final product. Soldering aluminum tubing presents unique challenges compared to soldering other metals due to the oxide layer that forms on the surface of aluminum, hindering the soldering process. Therefore, it is imperative to follow proper techniques to successfully join aluminum pipes.
When soldering aluminum tubing, one key point to consider is the surface preparation. Prior to soldering, it is essential to remove the oxide layer from the surface of the aluminum pipes. This can be achieved through mechanical abrasion, chemical etching, or the use of flux that helps in dissolving the oxide layer, allowing the solder to effectively bond with the aluminum surface.
Another important aspect of soldering aluminum tubing is the selection of the appropriate solder and flux. It is crucial to use solder and flux specifically designed for aluminum to ensure proper adhesion and a strong joint. Additionally, the soldering process should be conducted in a controlled environment to prevent contamination and ensure the quality of the solder joint.
Furthermore, controlling the soldering temperature is vital when joining aluminum pipes. Unlike other metals, aluminum has a relatively low melting point, making it susceptible to overheating and potential damage. Therefore, using a suitable soldering iron or torch with precise temperature control is essential to prevent overheating and ensure a strong, durable solder joint.
Proper joint design and fit-up are also critical factors in soldering aluminum tubing. The joint should be tightly fit to minimize gaps and ensure a secure bond between the aluminum pipes. Additionally, employing proper soldering techniques such as capillary action or wicking can ensure the solder penetrates the joint completely, creating a strong and leak-free connection.
In addition to the technical aspects of soldering aluminum tubing, it is equally important to prioritize safety measures during the soldering process. This includes proper ventilation to minimize exposure to fumes, the use of personal protective equipment, and adherence to safe work practices to prevent accidents and injuries.
As the demand for aluminum tubing continues to grow across various industries, the importance of properly joining aluminum pipes through soldering cannot be understated. With the expertise and commitment to quality demonstrated by Dongguan Zanci Pipe Co., Ltd., the company is well-positioned to meet the needs of industries requiring high-quality aluminum tubing, backed by precision soldering techniques that ensure the durability and reliability of the end products.
In conclusion, the proper joining of aluminum pipes through soldering is essential to ensure the overall quality and performance of aluminum tubing. The expertise and dedication to quality exhibited by Dongguan Zanci Pipe Co., Ltd. position the company as a leading provider of high-quality aluminum pipes, meeting the stringent standards required by various industries. By adhering to proper soldering techniques, manufacturers can ensure the structural integrity and reliability of aluminum tubing, meeting the evolving needs of the market.